Speaker Plastic Casing Injection Molding: Process and Suggestions
Overview
Currently, the materials used for speaker casings are in the following order: plastic, wood, and metal.
The application of plastic casings is becoming increasingly widespread due to its numerous advantages, including lightweight, portability, design versatility, good mechanical properties, durability, excellent insulation, and compliance with environmental policies.
As a result, it has become the preferred choice for casing among the manufacturers.
Casing injection molding is the first step in the entire manufacturing process.
Let's take a brief look at the entire process.
Part1: What Is Plastic Injection Molding?
Plastic injection molding is a common processing method where melted material is injected into a mold under high pressure and cooled to form the desired parts.
In the manufacturing of speakers, injection molding is widely used to produce critical components such as top plates and buttons.
The equipment used includes hydraulic machines and electric ones.
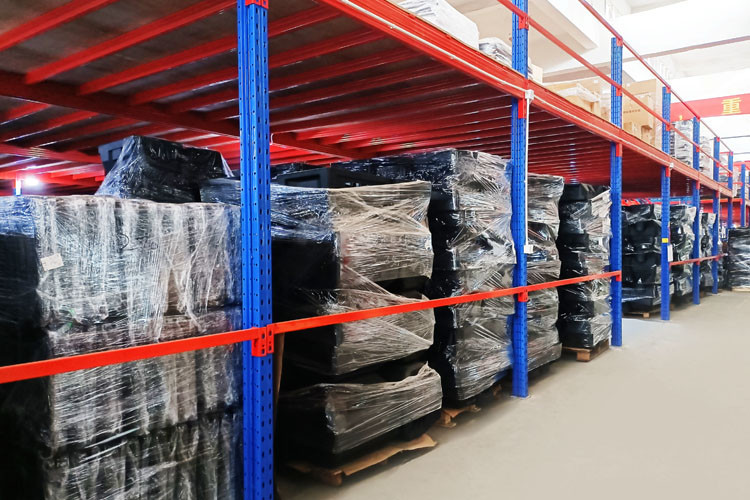
PP Shells in AUSMAN Repository
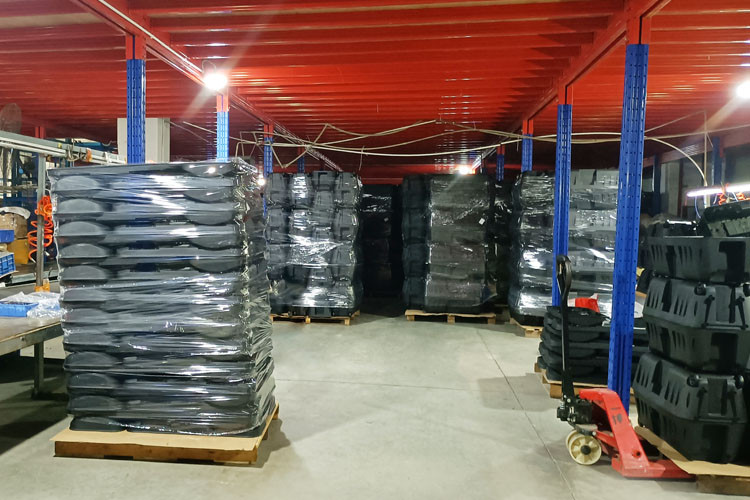
PP Enclosures On Assembling Line In AUSMAN
Part2: Main Types of Plastic Materials for Injection Molding
Speaker plastic casings usually employ durable, lightweight, and cost-effective materials. They are ABS (Acrylonitrile Butadiene Styrene), PP (Polypropylene), PC (Polycarbonate), and Acrylic.
These materials possess excellent mechanical properties and weather resistance, meeting the requirements for strength and appearance of casings.
And PP is the most widely used due to its excellent cost-performance ratio.
We get more information about enclosure material on these posts.
Part3: The Production Process
Initially, the mold design is developed according to the design requirements of the casing. The precision of the mold is critical to the quality of the injection molding.
1. Mold Design
Initially, the mold design is developed according to the design requirements of the speaker casing. The precision of the mold is critical to the quality of the injection molding.
2. Material Feeding and Melting
Selected plastic pellets are added to the hopper of the injection machine and melted at high temperatures, forming a molten state ready for injection into the mold.
3. Injection Molding
The molten material is injected into the mold cavity under high pressure. After cooling, the mold opens, and the molded casing is taken out.
4. Part Removal and Processing
After removing the molded casing, subsequent processes are carried out, including removing supports, trimming, and handling surface defects.
Step1. Mold Design
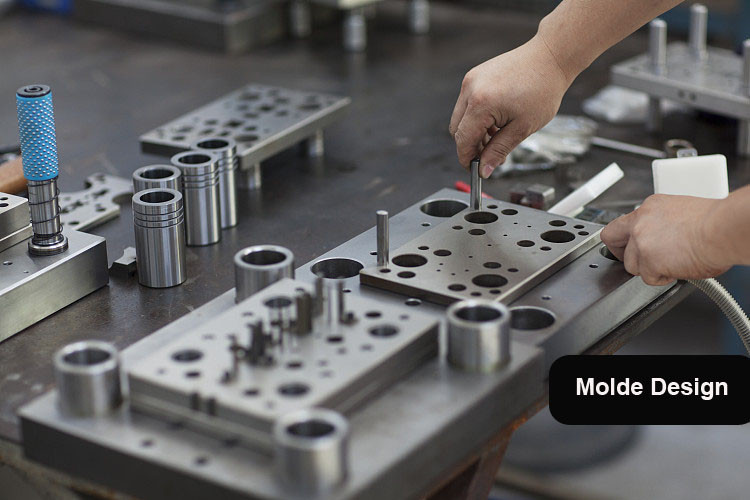
Step2. Material Feeding and Melting
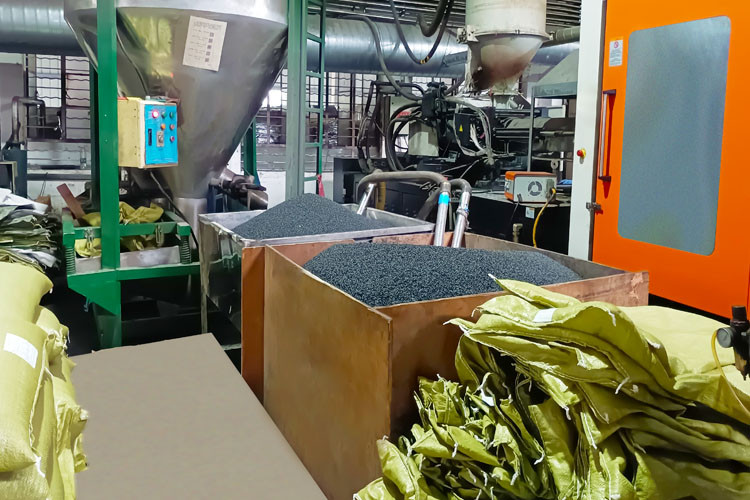
Step3. Injection Molding
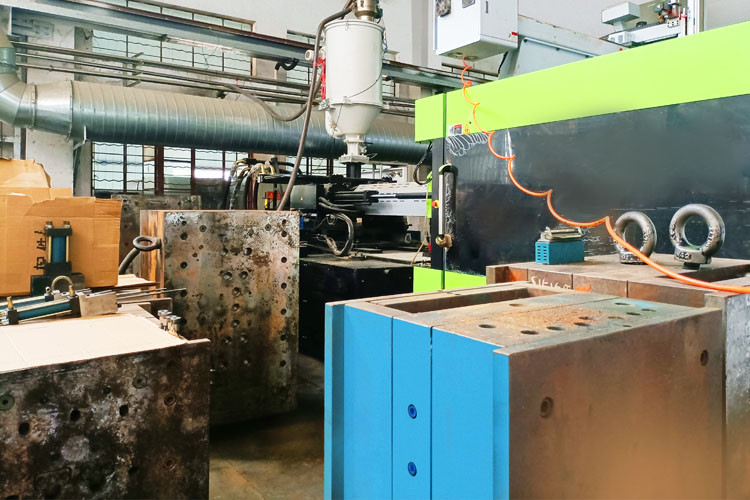
Step4. Part Removal and Processing
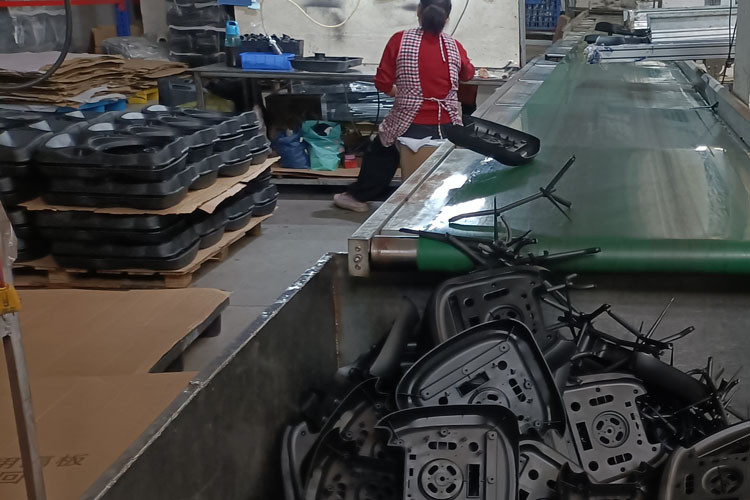
Part4: Suggestions About The Production Process
After removing the molded speaker casing, subsequent processes are carried out, including removing supports, trimming, and handling surface defects.
1. Temperature
Stable temperature control of the injection machine is essential to avoid uneven or overheating of the enclosures, which could lead to deformation of the final product.
2. Pressure
Strict control of injection pressure ensures that the mold cavity is adequately filled with plastic, preventing the formation of bubbles or short shots.
3. Mold Maintenance
Regular inspection and maintenance of the mold are necessary to maintain its precision and durability, extending its lifespan.
4. Quality Inspection is Necessary
Quality checks are performed on the molded casings to ensure accurate dimensions, smooth surfaces, and compliance with design requirements.
Conclusion
plastic injection molding is a commonly used process in the manufacturing of casings.
Selecting the right material and employing the correct process flow are crucial for obtaining high-quality, durable, and aesthetically pleasing casings.
AUSMAN Audio's Manufacturing History
If you have a sourcing requirement for molding from Chinese factories, please contact AUSMAN Audio China.
We are a professional manufacturer that supports customized and export services for all types of speakers (including OEM or ODM).
l l Related Reference Resources: